The Essentials of Arc Flash Labeling: A Step-by-Step Guide
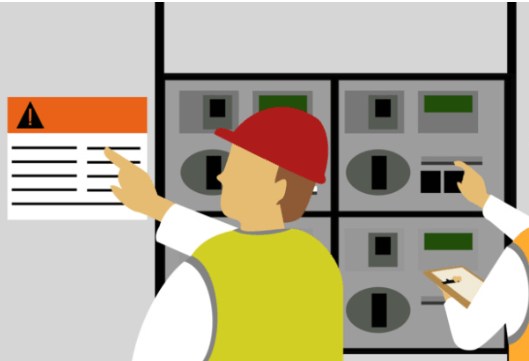
Arc flash labels are an important factor in workplace safety for anyone exposed to electrical power lines. An arc flash is a potentially explosive discharge of energy that occurs through the air from an electrical fault and may cause severe burns, injuries, and sometimes death. Lack of adequate instructions on labeling may lead to serious complications, placing worker’s lives in such a high risk due to these dangerous incidents.
Besides protecting individuals, arc flash labels contribute to the adherence to safety regulations. OSHA and NFPA classify electrical equipment and make it mandatory that facilities should install signals that warn the workers. Through these guidelines, the companies will easily avoid all the risks of accidents and hence prevent all the penalties—which are very costly.
Arc Flash Labeling: Step-by-Step
Step 1. Organize an Arc Flash Risk Assessment
Prior to labeling, an effective arc flash risk analysis has to be carried out. This determines the degree of risk of each electrical equipment and is usually prepared by a licensed electrical engineer. The findings inform which labeling is necessary as it establishes other aspects such as the arc flash boundary, the incident energy level, PPE to be used etc.
See also: Everest Base Camp Trek In March
Step 2. Determine Label Content
After that, the content of the label can be determined. At a minimum, labels should include:
a. Incident Energy Level
Estimates energy vulnerability issues, usually depicted in calories per square centimeter (cal/cm²).
b. Arc Flash Boundary
The area from the electrical equipment in which a person can be exposed to an arc flash that would cause a second degree burn.
c. Required PPE
Describes the PPE that is necessary to put on before approaching the equipment; for example, a face shield, gloves, or flame retardant clothing.
Step 3. Place Labels Correctly
Tags have to be attached to the external surfaces of equipment and be easily visible—normally, it is on the front side of the device. Simply put, the labels have to be strong, clear and withstand conditions such as heat, humidity, and light degradation.
Step 4. Use Color Coding and Symbols
Working in a hazmat environment requires discriminating quickly between levels of hazard, and bright colors and warning symbols assist in this regard.
Step 5. Regularly Update Labels
It is recommended that arc flash labels be reviewed and revised depending on the change in arc flash hazard levels caused by changes in equipment or system layouts. In this context, it is best that the labels are updated as often as possible, so that they reflect the current conditions and risks. According to the NFPA 70E, a new examination of arc flash risks should be done at least once in 5 years; sooner if you made any changes to the system.
Key Takeaways for Effective Arc Flash Labeling
To maximize workplace safety, arc flash labeling should:
a. Be based on an extensive arc flash evaluation.
b. Show energy levels and personal protection gear, define limits.
Completing each of these points guarantees that arc flash labels are both legally compliant and can offer protection to all workers who come into contact with electrical equipment.