Exploring the Versatility of Black Tin in Industrial Manufacturing
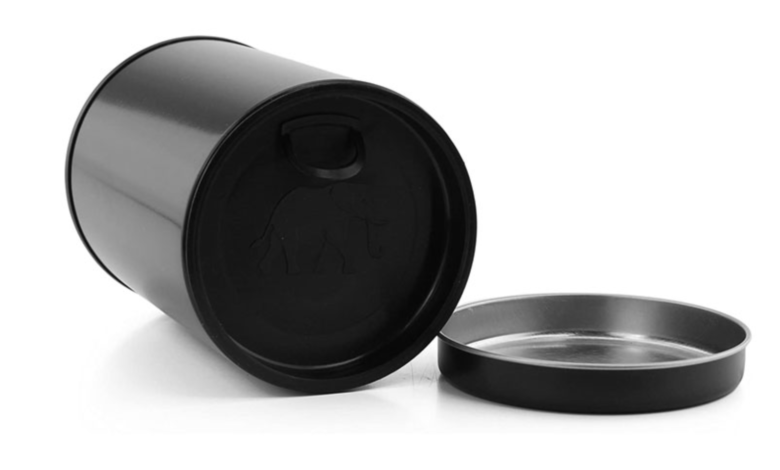
Black tin, a term often used to describe a specific form of tin oxide (SnO2) or tin alloys treated to achieve a dark appearance, has gained significant attention in industrial manufacturing. Its unique properties and versatility make it a valuable material in various applications, ranging from electronics to coatings and beyond. This article delves into the multifaceted uses of black tin, its manufacturing processes, and its impact on modern industries.
Properties of Black Tin
Chemical and Physical Characteristics
Black tins primarily refer to tin oxide (SnO2), which possesses remarkable chemical and physical properties:
- High Melting Point: SnO2 has a melting point of around 1630°C, making it suitable for high-temperature applications.
- Electrical Conductivity: In certain forms, tin oxide is conductive, which is advantageous for electronic components.
- Chemical Stability: It is resistant to corrosion and oxidation, ensuring longevity in various environments.
- Mechanical Strength: Tin oxide is hard and durable, making it ideal for protective coatings.
Aesthetic Appeal
The dark, lustrous appearance of black tin makes it aesthetically appealing for decorative purposes in addition to its functional uses.
Manufacturing Processes
Smelting and Refining
The production of black tin involves several stages:
- Ore Extraction: Tin is extracted from its ore, cassiterite (SnO2), through mining.
- Smelting: The ore is then smelted to produce crude tin.
- Refining: Crude tin is refined to remove impurities, resulting in pure tin or specific tin alloys.
Oxidation
To produce black tin oxide, the refined tin undergoes controlled oxidation processes:
Thermal Oxidation: Heating tin in the presence of oxygen forms a layer of tin oxide.
Chemical Vapor Deposition (CVD): A more controlled method where tin reacts with oxygen in a vapor phase to form a uniform tin oxide layer.
Alloying
Creating tin alloys involves combining tin with other metals (e.g., copper, zinc) to enhance specific properties:
Bronze (Tin and Copper): Used in bearings, gears, and various industrial components.
Pewter (Tin and Antimony/Copper): Common in decorative items and tableware.
Applications in Industrial Manufacturing
Electronics
Black tin oxide plays a crucial role in the electronics industry:
Semiconductors: Used in thin-film transistors and diodes due to its electrical conductivity.
Transparent Conductive Coatings: Applied to display screens and solar cells for their conductive and transparent properties.
Soldering: Tin alloys are used in soldering materials, providing strong and reliable joints for electronic circuits.
Coatings and Platings
Tin oxide is widely used for its protective and decorative qualities:
Corrosion Resistance: Applied as a coating to protect metals from oxidation and corrosion.
Decorative Plating: Used in jewelry and hardware for its aesthetic appeal and durability.
Food Packaging: Tin-plated steel cans preserve food by preventing corrosion and maintaining food safety.
Automotive Industry
In the automotive sector, black tin has several applications:
Engine Components: Tin alloys are used in bearings and bushings due to their low friction and wear resistance.
Coatings: Protective coatings on automotive parts enhance durability and resistance to harsh environments.
Renewable Energy
Tin oxide is instrumental in advancing renewable energy technologies:
Solar Cells: Transparent conductive oxides are essential for photovoltaic cells, improving their efficiency.
Battery Technology: Tin-based anodes in lithium-ion batteries offer higher energy densities and better performance.
Glass Manufacturing
Tin oxide coatings are applied in the production of glass:
Low-E Glass: Improves energy efficiency in buildings by reflecting infrared radiation while allowing visible light to pass through.
Conductive Glass: Used in touchscreens and smart windows.
Advantages of Black Tin in Manufacturing
Durability and Longevity
Black tin coatings and components exhibit excellent durability, reducing the need for frequent replacements and maintenance.
Cost-Effectiveness
Tin and its compounds are relatively abundant and cost-effective, making them attractive for various industrial applications.
Environmental Benefits
Tin is non-toxic and recyclable, contributing to sustainable manufacturing practices and reducing environmental impact.
Challenges and Limitations
Production Costs
While it is cost-effective, producing high-purity tin oxide and specialized tin alloys can be expensive.
Technological Limitations
Advances in processing technologies are needed to fully exploit the potential of black tin in emerging applications, such as flexible electronics and advanced energy storage.
Market Fluctuations
The tin market is subject to fluctuations in supply and demand, which can impact the availability and price of tin-based materials.
Future Prospects
Technological Innovations
Ongoing research and development efforts are focused on enhancing the properties of black tin and discovering new applications:
Market Growth
The demand for black tin is expected to grow in various sectors, driven by the increasing adoption of renewable energy technologies and the need for durable, high-performance materials.
Environmental Sustainability
As industries continue to prioritize sustainability, the role of non-toxic, recyclable materials like tin will become increasingly important in reducing environmental impact.
Drive the development of various industries
Black tin’s versatility in industrial manufacturing stems from its unique combination of chemical, physical, and aesthetic properties. From electronics to renewable energy and beyond, its applications are diverse and continually expanding. As technological advancements and market demands evolve, black tin is poised to play a crucial role in the future of manufacturing, offering innovative solutions and sustainable practices. The ongoing research and development in this field promise to unlock new potentials and drive further success in various industries.