Importance of mould temperature controller for Injection Molding
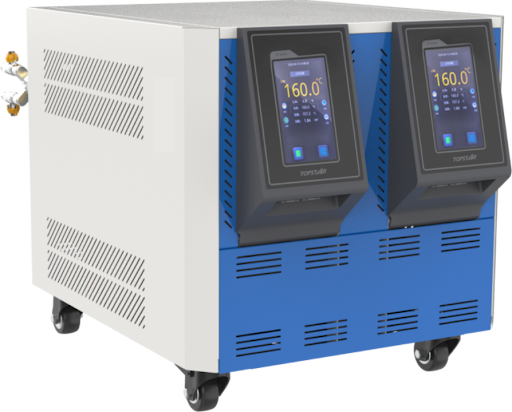
Injection molding is a versatile manufacturing process that precisely controls various parameters to produce high-quality plastic parts. Among these various injection molding parameters, mold temperature determines the final performance and appearance of the molded part. We can control the temperature well through the mold temperature controller to achieve the final ideal performance. Below, we will tell you the importance of mould temperature controller in optimizing the injection molding process.
Improve part quality and consistency
One of the main functions of the mould temperature controller is to maintain the consistency and uniformity of the temperature distribution throughout the mold cavity during the injection molding process. Consistent mold temperature can achieve uniform part quality, reduce defects, and ensure dimensional accuracy. Variations in mold temperature can cause problems such as warping, sink marks, and surface defects, which can compromise the integrity and aesthetics of the molded part. Temperature controllers can precisely control mold temperature, alleviate these problems, and ensure consistent part quality every time. Maintaining optimal mould temperature is crucial for producing automotive parts, consumer electronics, or medical devices.
Improve production efficiency and cycle time
In addition to improving part quality, mold temperature controllers can improve production efficiency and shorten injection molding cycle time. Controlling mold temperature helps promote faster cooling and solidification of molten plastic, thereby reducing cycle time and increasing productivity. By shortening the cooling time required for each cycle, mold temperature controllers enable manufacturers to achieve higher output while increasing machine utilization. After shortening cycle time, energy consumption and operating costs associated with heating and cooling processes can also be reduced. Help optimize energy efficiency by maintaining precise temperature levels and reducing heat loss during molding.
Mould temperature controller facilitates process control and optimization
For greater control and flexibility, mold temperature controllers can optimize the injection molding process to meet specific production requirements. Adjusting mold temperature to accommodate different materials, part geometries, molding conditions, part quality, cycle time, and overall process efficiency can optimize the process. In addition, mold temperature controllers enable users to try different molding parameters and techniques to improve process robustness and repeatability. By fine-tuning the mold temperature profile, manufacturers can determine the optimal settings to achieve the highest quality parts with the tiniest scrap.
Mould temperature controller Prevent Thermal Stress and Mold Damage
Maintaining proper mould temperature is critical to preventing thermal stress and potential damage to the mold during the injection molding process. Rapid temperature fluctuations or uneven heating and cooling can cause thermal shock, leading to premature wear and degradation of mold components. This affects part quality and increases the risk of mold maintenance and replacement, resulting in downtime and production delays. Create multi-cavity molds to produce multiple parts per cycle, significantly increasing the production capacity of your injection molding machine. By maintaining a stable temperature within the desired operating range, temperature controllers help extend the life of the mold and reduce the need for expensive repairs or replacements.
Achieve Material Compatibility and Processing Versatility
Different thermoplastic materials have specific processing requirements and performance characteristics that must be carefully managed during the injection molding process. Mould temperature controllers can help by providing precise temperature control that targets the unique properties of each material. Whether processing commodity plastics, engineering resins, or high-performance polymers, temperature controllers help optimize processing conditions to achieve the desired part quality and performance.
In addition, mould temperature controllers can adapt to different molding technologies and applications, allowing users to explore processing versatility and flexibility. Whether using traditional injection molding, gas-assisted injection molding, or over-molding, it can provide the necessary temperature control to accommodate various production requirements.
Get High-Quality Products
Mould temperature controllers are vital in optimizing the injection molding process by improving part quality, increasing production efficiency, facilitating process control, preventing thermal stress, enabling material compatibility, and improving safety and reliability. Temperature controllers help manufacturers achieve consistent and high-quality parts by maintaining precise and uniform mold temperatures.