Introduction of Heat Transfer in Fluids Using ANSYS Fluent
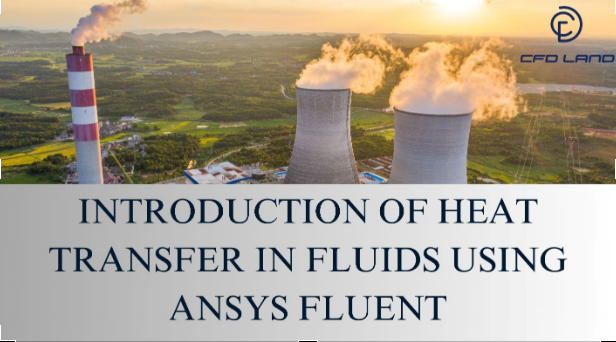
In many industries, heat transfer is an influential issue that engineers consider in their designs. Look around yourself, the refrigerator radiator, which is a type of heat exchanger, is designed to maximize heat transfer, while the body of the refrigerator is designed as a thermal insulator. In the design of your house, efforts have been made to minimize heat transfer with the outside environment so that it stays warm in winter and cool in summer.
There are different methods to assess heat transfer in a system, and one of the most useful methods for determining the smallest details of the system is CFD heat transfer simulation. If you have been working with this method for a while, you are likely familiar with ANSYS Fluent, a powerful software that can be used for all simulation tasks. To see the capabilities of this software in the field of heat transfer, take a look at cfdland.com. Many CFD heat transfer projects have been completed on this site, ranging from HVAC systems to heat exchangers, and the variety and number of projects are extensive.
Types of Heat Transfer
Heat transfer has 3 mechanisms:
- Conduction: Heat transfer without mass transfer is called conduction. This model is the only method of heat transfer in solids, but it can also occur in fluids.
- Convection: Heat transfer involving mass transfer is called advection, while heat transfer without mass transfer is called conduction. The combination of these two processes is referred to as convection. This type of heat transfer occurs in fluids. If the fluid flow is caused by an external factor, such as a pump, it is called forced convection; if the fluid flow is due to temperature differences and density differences, it is called free convection.
- Radiation: Due to the vibration of subatomic charged particles, the material itself emits electromagnetic waves. When these waves collide with other charged particles, they cause them to vibrate and increase their temperature. In this method of heat transfer, there is no need for mass to transfer heat; in other words, electromagnetic waves can move through a vacuum.
Heat Transfer in Fluids using ANSYS Fluent
In fluids, all three mechanisms of heat transfer can occur simultaneously, or only conduction can occur if the fluid don not move. Therefore, CFD heat transfer simulation can be simple or very complex. Apart from the existing heat transfer methods in the problem, fluid movement introduces additional complications to the simulation that greatly affect heat transfer, such as:
- Flow regime: In Fluent software, there are many options for the viscosity equation. The fluid can be considered to have zero viscosity, which is called “inviscid.” If the fluid viscosity is not zero, the flow regime can be either laminar or turbulent. In many industrial applications, fluid flow is turbulent. This regime significantly increases the amount of heat transfer. Various methods are available in Fluent for simulating turbulent flow, which the user can choose according to the needs of the problem and the available computing power.
Material properties can be defined by different methods in ANSYS Fluent and each of them can be introduced as a function of different parameters. For example, for buoyancy-driven flows, the density can be defined using the Boussinesq model and using the thermal expansion coefficient.
- Multiphase flow: In many cases, multiple phases of matter are present in the system, such as liquid and gas, or solid particles floating in the fluid. This type of simulation has its complications, and various CFD methods, such as Discrete Phase Model (DPM), are used for its simulation.
- Boundary layer: The area near the solid surface where the fluid velocity decreases rapidly is called the boundary layer. This area strongly affects the heat transfer between the solid and fluid surfaces. Engineers increase heat transfer in this area by using various methods, such as creating turbulent flow. The details of the simulation of this area are very important; that’s why the mesh in the boundary layer is much finer than in the rest of the simulation domain.
- Phase change: One of the phenomena that can occur with heat transfer is phase change. Due to the constant temperature and the absorption of latent heat by the material during the phase change, this phenomenon strongly affects the thermal behavior of the system.
Read Also: Protect Your Home From Hail Damage With Smart Fixes
“Greenhouse Ventilation Considering Relative Humidity CFD Simulation” is just one of the many projects carried out on CFDLAND.com in the field of CFD heat transfer simulation.
Conclusion
CFD heat transfer simulation is one of the methods that engineers use to design many industrial systems. This simulation model can be very simple or very complex, depending on the details and phenomena present in it. ANSYS Fluent software can handle even the most complex simulations. To see the capabilities of this software, visit the projects done with it at CFDLAND.com. I assure you that you will be surprised by those projects.